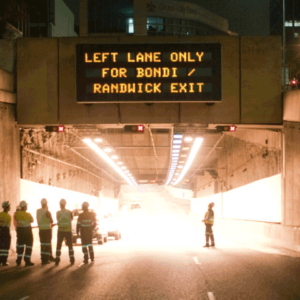
Variable Message Signs (VMS) are instrumental in providing situational awareness to motorists. Providing notification of incidents, trip information, route advisory and other valuable information such as civil notices and community information. Being charged with running 24 hours per day, 7 days a week.
However, no system is immune from moments of failure, error or disruption. In this case, maintenance is a key consideration to extend the mean time between failure, limit mean down time (MDT) and keep a VMS running at maximum cost-effectiveness and functionality.
The cost of maintaining a functional element of infrastructure becomes an important factor for asset managers. Variable Message Signs (VMS) are a key component of any interconnected and intelligent traffic management system. As part of a comprehensive risk management appreciation, maintenance becomes a key focus in mitigating the risk of down time and reducing the likelihood of faults.
A recent review on VMS maintenance, found that the mean time between faults (MTBF) was 16 days and had an average frequency of 28 faults per year. This resulted in a considerable maintenance cost relating to labour and equipment. As well as an assumed cost effect to motorists utilising the infrastructure due to delay or disruption.
As it stands the current accepted service life of a VMS is 10 years. Be that as it may, achieving a high percentage of functionality over this time is about minimising failure. Generally speaking, VMS failure modes are classified into five (5) categories:
- Communications
- Display
- Hardware
- Power
- Mechanical
Factors Affecting Functionality
In considering what factors affect functionality, a trichotomy of appreciation is required to look at 1.) the reliability and endurance of the system and its components; to maximise the mean time between faults, 2.) the maintainability; to maintain and preserve the functionality of the VMS for its service life, and 3.) the ease of accessibility; including response times and minimalisation of disruption to motorists.
Reliability Maintainability Accessibility
Reliability
Complex systems are only as reliable as the weakest aspect of their component parts. As such it is paramount that the choice of materials and components to be integrated, are on par with or exceed the functionality and durability expectations of the application. In the case of VMS, the system is practically an ‘always on’ scenario. As such, any gradual deterioration must be minimised. With durability of all components to align with the life expectancy of the system as a whole. Where this is not possible, it is important that the restoration or replacement of component parts is incorporated into a program of scheduled maintenance.
Many variables come into the manufacturing of a high value product for traffic applications. For example, Armitage Group achieves enhanced durability of optics by taking an extra protective measure of integrating a punch hole matrix into the enclosures of variable message signs (VMS). Thereby minimising ultra-violet exposure to the polycarbonate and LEDs; of which have 90,000+ hour life as a minimum.
Wind induced flexion of VMS panels is mitigated by the decision to use either stainless steel or aluminium enclosures, with high rigidity that greatly reduces deflection. Thereby, maintaining the integrity of weather seals and preventing water ingress over time. Together with the application of hard-wearing powder coating which well exceeds minimum requirements. Together with being a matt finish that minimises reflection on the sign, enhancing the signs optical clarity in a tunnel environment.
Involved in the entire chain from production to installation, Armitage Group strives to add value to the customer at each opportunity for enhancement, confirming specifications meet or exceed project specific requirements. For example, specifying the alloy type and methodology of welding to maximise durability, or ensuring that the LEDs are soak tested at full luminosity for a minimum of 72 hours during a regimented factory acceptance testing process. Affording a layer of quality control and reducing the risk of new product failures for the customer post installation.
Maintainability
In consideration of VMS maintainability post installation, we must first consider that maintenance generally falls into either a pro-active or re-active categorisation. In view of functionality, the overall risk of down time can be mitigated in part through a combination of measures, including elimination, substitution and engineering. For example, elimination of ingress of moisture, substitution of power through battery backup and engineering of redundancy into the system. Equally important, from an operational perspective, pro-active maintenance aims to minimise the occurrence errors and hence down time.
Firstly, similar to the servicing of a car, regular preventative maintenance ensures that the system is working efficiently whilst components are tested or inspected to validate functionality. Preventative maintenance inspections are also a valuable opportunity, to identify any potential indications of deterioration that need addressing and preserve functionality.
Secondly, predictive maintenance takes a historical and data driven approach. Provisioning for the mitigation of historical failures or accepted deterioration of certain components. This highlights the value of keeping an accurate and time stamped failure log, to provide insight into the nature and frequency of errors. Allowing a closed loop of information where historical data is considered into functionality and the concurrent creation of data keeps this resource current and relevant.
Thirdly, as not all materials and components are equally matched in service life, scheduled restoration or replacement supplements inspections and maintenance, to mitigate the risk of failure of individual components. Ensuring these items are addressed at the opportunity presented by a preventative maintenance inspection, will minimise the chance of inducing failures by over-maintaining and creating unnecessary wear and tear and disruption to functionality.
Fourthly and holistically, reliability centred maintenance(RCM) looks at criticality factors such as safety and environmental considerations, traffic flow interruption, repair expense, the effect on other systems and redundancy. With safety always being the number one consideration, the RCM process aims to prepare the operational context in the development of a pro-active maintenance schedule. Assessing functions and functional failures, identifying failure modes and their associated effects and classifying the criticality of failure consequences into safety, environmental, operational and non-operational significances. With the intention of employing the right kind of maintenance at the right time, by the creation of default strategies that asset managers can implement as part of complete maintenance plan.
Finally, In the event that a failure does occur, a call-out event will be triggered, in which re-active maintenance crews will have to attend, assess and rectify the fault presented. All of which contribute to the mean down time (MDT) and in any event a lowering of safety mitigation measures. Hence the ease of accessibility plays a role in lowering response time and enabling expediated maintenance and repair.
Accessibility
To ensure ease of accessibility to and within the traffic management asset, these considerations are included in the design process. Always upholding a customer-focus, Armitage Group often engages in a co-creation and certification process with stakeholders. Integrating design features that enable efficient field access, ease of maintenance and expedited repair.
Functionality
The saying ‘if it is not broken, don’t fix it’ may induce caution. With this in mind, it is important when considering regular scheduled maintenance that we don’t induce failures. Therefore, through careful consideration of the maintenance approaches described, a maintenance schedule can be generated that incorporates a synchronisation of tasks to prevent unnecessary maintenance events. Consequently, extending the mean time between failures and maximising the percentage functionality for the asset.
Asset Management
As can be seen, asset managers have a lot of factors to consider regarding maintenance of traffic management systems. Tasked with ensuring functionality, appropriate cost-benefit based decisions and the creation of maintenance schedules that meet project requirements customer expectations and prolong asset life. On balance, thoughtful integration of a harmony of maintenance approaches can ensure that the right kind of maintenance is performed at the right time. Culminating in a functional and reliable VMS solution.
Further Information
For a deeper dive into the subject of Variable Message Sign specifications, reliability centred maintenance and maintenance considerations, see the following literature.
Luk, J.Y., Li, J. and Wazirzada, Q., 2015. Reliability-centred maintenance for variable message signs: a feasibility study.